Hydrogen has been called the “Swiss army knife” of decarbonisation because it can do many things. But not all of them make sense.
Today, the world uses about 100 megatonnes of hydrogen per year (MT/y), but this is produced almost entirely from fossil fuels. To use hydrogen for decarbonisation, we must shift to emissions-free forms.
Global forecasts for green hydrogen produced from renewable sources vary widely, ranging from today’s demand (100 MT/y) to an optimistic 700 MT/y by 2050. Bloomberg’s recent 2050 forecast suggests a downward trend. Even so, shifting today’s demand to green hydrogen poses significant challenges.
In our research, we use the “clean hydrogen ladder” to sort and quantify different uses of green hydrogen.
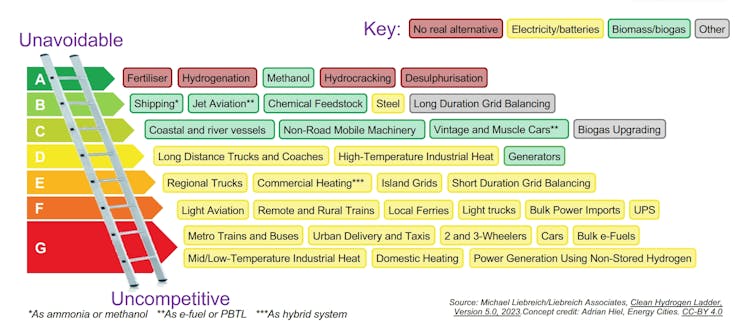
Hydrogen demand in New Zealand
Our research shows New Zealand’s total demand for green hydrogen would be around 2.8 Mt/y if all technically feasible applications switched to hydrogen. If we prioritise uses where green hydrogen is the only decarbonisation option, demand would be up to 1 MT/y.
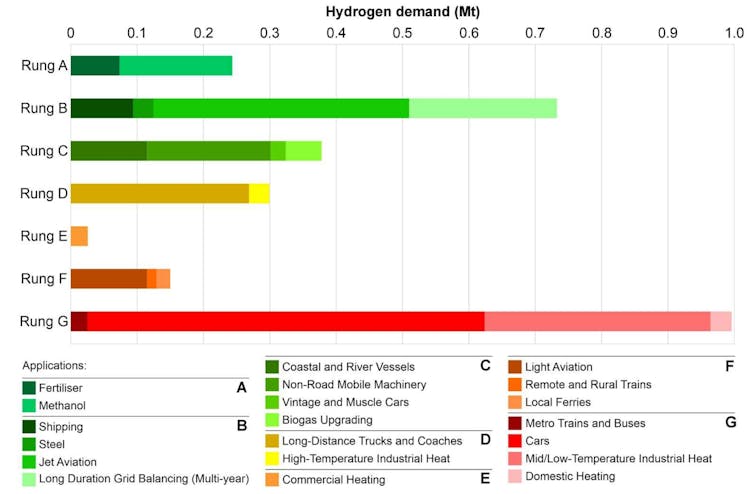
Fertiliser and methanol are at the top of the list. They are considered “unavoidable” because there are no other alternatives for decarbonisation. Together, they would require about 0.2 MT/y.
Next on the list are things like shipping and jet fuel (through hydrogen-based synthetic fuels), steel production and long-term grid storage. These could add another 0.7 MT/y.
At the other end of the ladder is where hydrogen is uncompetitive because there are better alternatives, like battery electric cars or heat pumps.
To produce 1 MT/y of green hydrogen, New Zealand would need to triple the installed capacity of renewable power plants and build out a massive 10 GW of electrolysers (devices that uses electricity to obtain hydrogen from water).
Long-term hydrogen storage
A strategic use of hydrogen is long-duration storage to move cheap solar energy from summer to winter, beyond what hydropower reservoirs can balance.
Hydrogen can be stored in complex chemical structures, BBQ-sized tanks and gas tankers (ships). But very large amounts of hydrogen will need to be held underground, with depleted natural gas reservoirs offering the most promising sites.
There are several challenges to be addressed to transfer hydrogen into storage at three or more kilometres underground — and get it back up again. First, as a molecule, hydrogen is not well behaved. It tends to flow through materials that might contain it. This means we need to use specialised (expensive) materials along with careful leak detection.
Second, recent discoveries of thriving microbial communities in New Zealand’s gas fields raise the prospect of renewable gases becoming a food source for microbes rather than an energy source.
Ironmaking
Another pressing application for hydrogen is to decarbonise steel production (which accounts for eight per cent of global greenhouse gas emissions).
Today, coal is used to strip oxygen from iron ore and provide combustion heat. Renewable electricity could supply heat and hydrogen to replace coal. The so-called hydrogen-based direct reduced iron (H2-DRI) process is feasible at scale, as demonstrated by Midrex, HYBRIT and POSCO.
In collaboration with Victoria University of Wellington, in a project on zero-carbon production of metals, we found that electricity prices below NZ$0.13/kWh are necessary for hydrogen steel making to compete with the standard coal-based process. Solar PV is already significantly below these costs during daytime and close with battery backup.
Exporting hydrogen
New Zealand’s interim hydrogen roadmap suggests hydrogen exports of about 0.5 MT/y. Meeting domestic hydrogen demand is challenging enough, but export ambitions add another layer of complexity.
Hydrogen is difficult to transport because it is a very light gas that takes up a lot of space. But it can be densified. Previous research explored the feasibility of hydrogen exports from New Zealand, looking at cryogenic liquefaction, ammonia conversion and toluene hydrogenation.
Liquid hydrogen, while lower in cost, boils at minus 253°C and requires specialised insulated transport vessels, with notable losses expected from boil-off. On top of that, the infrastructure to ship large quantities of liquid hydrogen around the globe does not currently exist.
Ammonia, transported at minus 33°C, suffers less from boil-off and is more practical. Next-generation catalysts such as those from Liquium could make ammonia even more favourable. The third option, toluene-MCH, involves higher costs, but is being tested at a commercial scale in Japan.
Recent research highlights a fourth alternative, e-methanol produced from green hydrogen. E-methanol is promising because of its modularity and because we already know how to transport and store it. However, other researchers see e-methane as more promising as it could leverage existing port and pipeline infrastructures.
The cost of hydrogen
In terms of costs, hydrogen has a long way to go.
To reduce costs, electrolysers can be scaled up, though this increases equipment expenses and creates a trade-off between capital and operating costs. Additionally, electrolysers rely on expensive and scarce materials like platinum and iridium. Our research focuses on developing low-cost electrolysers by utilising earth-abundant materials.
Interestingly, other alternatives for emissions-free hydrogen are emerging. So-called “gold” and “orange” hydrogen (from natural accumulation or enhancement of olivine to serpentine, respectively) are good examples. Tantalisingly, New Zealand’s unique geology offers the potential of both finding “gold” and inducing “orange” hydrogen.
Ultimately, the success of hydrogen will depend on competitiveness against alternative solutions, mainly electrification and biofuels. For applications with no easy alternative, emissions-free hydrogen is a direct option.
Jannik Haas, Senior Lecturer of Sustainable Systems, University of Canterbury; Aaron Marshall, Professor of Chemical Engineering, University of Canterbury; Andy Nicol, Professor in Geosciences, University of Canterbury; David Dempsey, Associate Professor in Natural Resources Engineering, University of Canterbury; Ian Wright, Professor in Marine Geology, University of Canterbury; Matthew J Watson, Professor in Chemical Engineering, University of Canterbury, and Rebecca Peer, Senior Lecturer in Natural Resources Engineering, University of Canterbury
This article is republished from The Conversation under a Creative Commons license. Read the original article published Nov. 24, 2024.