Revolutionizing the building blocks of construction
In July 2021, the National Carbon Capture Center (NCCC) announced its first carbon dioxide (CO2) utilization test as the facility successfully demonstrated the production of ultra-low-carbon concrete using an innovative technology – the UCLA CarbonBuilt team’s NRG COSIA Carbon XPRIZE-winning process – which reduced the embodied carbon intensity of concrete masonry by more than 50%.
Project teams from the NCCC (managed and operated by Southern Company), the UCLA Samueli School of Engineering and UCLA startup CarbonBuilt utilized CO2, taken directly from fossil-based flue gas streams to cure over 5,000 concrete blocks. The multi-week test proved that CarbonBuilt’s technology produces performance-equivalent, functional replacements for traditional concrete products.
An additional round of testing would leverage the initial learnings to identify ways to enhance concrete carbonation efficiency and help expand the product range.
Ultra-low-carbon concrete technology commercialization
Less than a year after the initial test, CarbonBuilt’s low-carbon concrete process went into real-world production when Blair Block agreed to utilize the newly created technology at its concrete masonry production facility in Childersburg, Alabama. The first converted line at Blair Block will avoid at least 2,000 tonnes of CO₂ emissions plus remove more than 500 tonnes of atmospheric CO2 per year.
CarbonBuilt also recently announced its solution to achieve clean concrete – concrete made without using any ordinary portland cement (OPC) at all. By eliminating OPC, a carbon-intensive binder in concrete products, CarbonBuilt believes that carbon-neutral, if not carbon-negative, concrete blocks are possible.
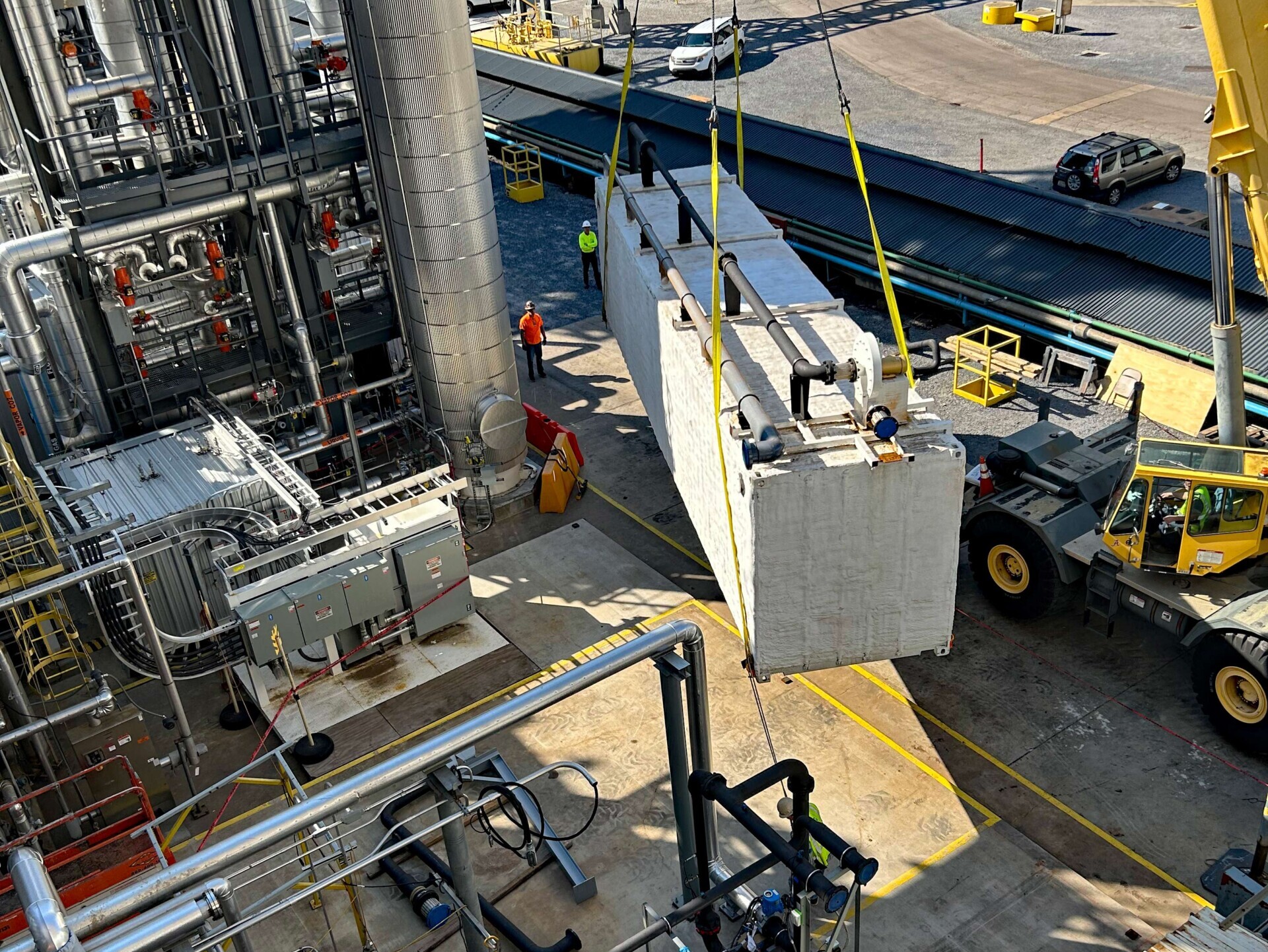
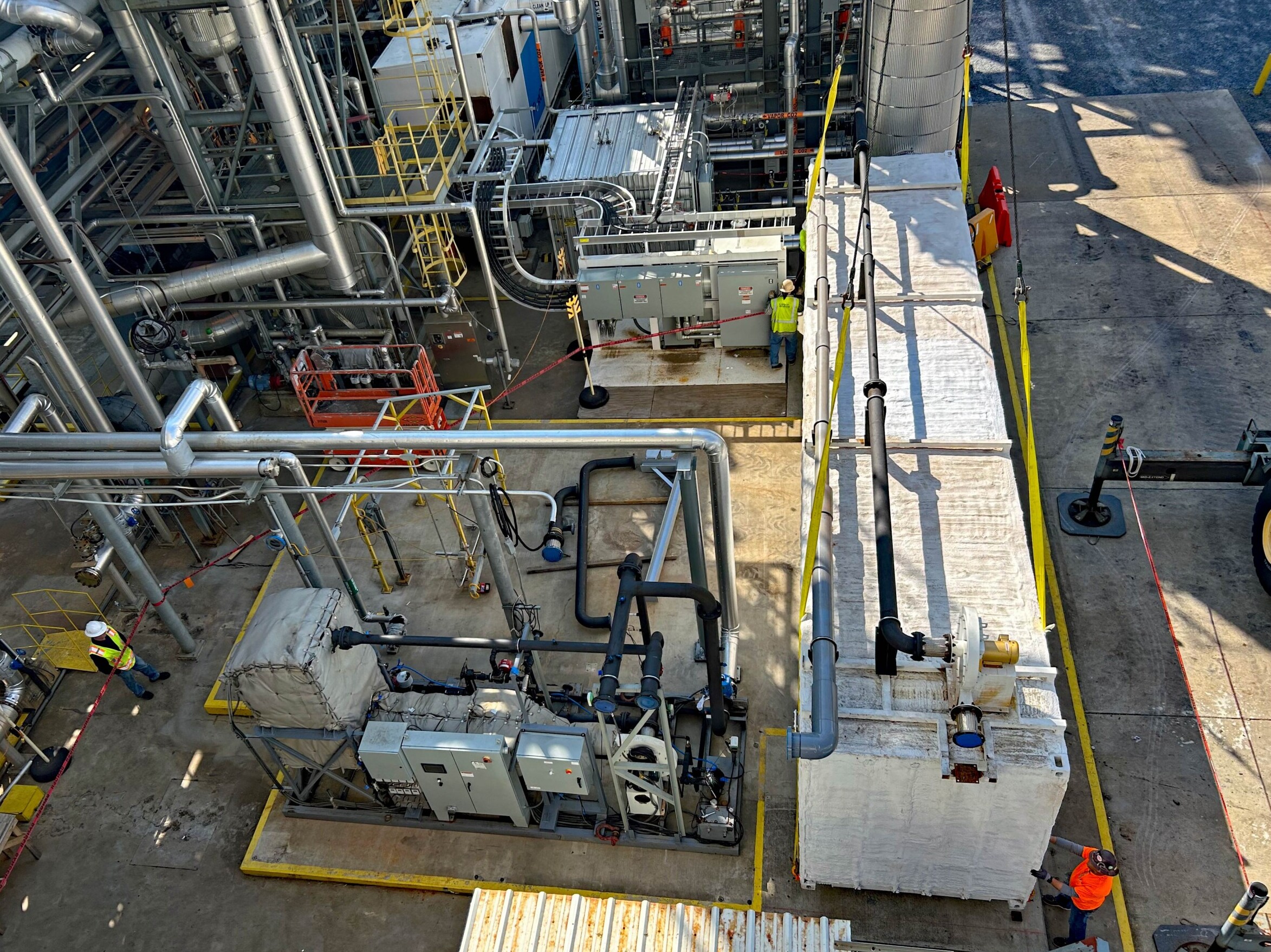

Next NCCC test aims to improve concrete carbonation efficiency, expand product range
Fast forward to the spring of 2024. UCLA’s research team is once again at the NCCC to expand on its initial product testing. In addition to the concrete masonry units (CMU) that were successfully demonstrated in 2021, two more use cases – segmental retaining wall (SRW) and concrete manhole (CM) products – will be demonstrated.
The concrete production testing is expected to begin in May 2024 and is projected to last approximately five weeks.
“Since UCLA’s process does not require an intermediate CO2 capture or separation step, it is much easier to be integrated into the commercial concrete production process,” said Tony Wu, principal engineer and project manager, NCCC. “The National Carbon Capture Center is looking forward to witnessing this improved curing process and to again provide full assistance during this upcoming test.”
The new testing will build on what the UCLA team learned in the first round of analysis. In addition to ongoing process improvements, higher rates of CO2utilization are expected. And, along with dry-cast CMU products, SRW and wet-cast CM products will be tested for the first time to gain knowledge on the different concrete products and the wet-cast concrete carbonation process.
“The collaboration between the National Carbon Capture Center and UCLA has enabled us to scale up our testing in real-world settings so we could fine tune our approach to fit the need of industry,” said UCLA project team lead and the Pritzker Professor of Sustainability Gaurav Sant. Sant, who leads UCLA’s Institute for Carbon Management, founded UCLA startup CarbonBuilt in 2020 and holds faculty appointments in civil and environmental engineering and materials science and engineering at UCLA. “With additional testing, we look forward to optimizing both carbon capture and utilization for an even more sustainable and affordable carbon-neutral solution.”
Looking ahead
The NCCC, UCLA and CarbonBuilt’s groundbreaking research and testing represent a significant step forward in decarbonized construction practices and are a testament to the power of collaboration, innovation and dedication to sustainable solutions. The learnings from these tests will be used to help reshape the industry and pave the way for a more sustainable, carbon-neutral future in construction.
CCUS as key enabler of the net-zero future
So, how can carbon capture, utilization and sequestration (CCUS) be used to decarbonize hard-to-abate industrial processes like concrete production and the power industry?
CCUS is critical to achieving net-zero greenhouse gas (GHG) emissions due to its ability to capture carbon from vital sectors that are accepting the challenge to decarbonize. CCUS plays a principal role in today’s energy transition by using available resources while substantially reducing emissions.
Like other heavy industry sectors, the cement industry generates CO2 emissions as an inherent part of its production. The CarbonBuilt process reduces and replaces the carbon-intensive OPC in concrete production, reducing CO2emissions. Additionally, it utilizes CO2 sourced from industrial processes or atmospheric CO2, thereby permanently storing it in the finished concrete products. This “one-two punch” of avoidance and removal doubles the benefit of CarbonBuilt’s approach....
Read the full news release here